Complex turn-key project to power a Data Center in northern Europe
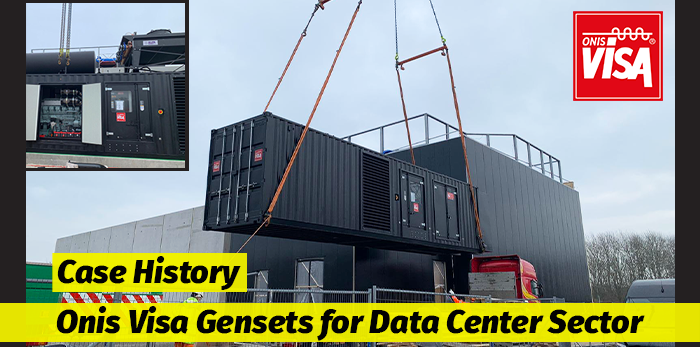
Visa SPA prides itself on offering complete and customized solutions for Data Centers. One of the most recent examples, was a project that Visa designed and completed for an important plant in northern Europe
The main objective of the project was specifically to supply reliable solutions to grant the plant to work in total safety, avoiding potential risky situations that could undermine the operating system. One of the customer’s most import requirement was in fact to rely on high quality products, engineering expertise and efficiency.
Two units of Onis Visa generating sets have been designed to guarantee uninterrupted power supply, a fundamental aspect to protect the stored data information.
The project started in January 2020 competing against some other manufacturers. Thanks to specific aspects, Visa was selected because it offered the best combination between reliability and sustainability of the units during maintenance and operations.
The temperature inside the data centre, including conditioning and proper ventilation for the storage devices, were relevant factors to be considered; they were protected by the same emergency backup generators, operating automatically in case of power failure, thus preventing any loss of data or functionality.
DATA | DESCRIPTION |
---|---|
Project: | DATA CENTER |
Location: | northern Europe |
Power required: | 2 units x 1730.0 kVA each (DCP power) |
Power installed: | 3470.0 kVA (DCP power) |
Generator sets: | 2 x M 1730 CONT 40' |
Dimensions: | 2438 x 13264 x 4921 mm (W x L x H) |
Special configuration:
Redundant starting system, double battery pack, each of them provided with a dedicated battery charger.
Special dry cooler for noise reduction. Double set of refueling pumps for appropriate redundancy. Double controllers.
Purpose:
To prevent any loss of data and/or functionality of the databases to ensure the highest level of security.
To fulfill the specific requirements, the Visa SpA engineering team appointed for developing the project selected 2 units of model M1730 CON.
Technical specifications:
Generating sets are equipped with 16-cylindered Mitsubishi engine coupled with oversized Meccalte alternator managed by InSync controller.
Units are installed in a 40’ container, guaranteeing 70 dBA at 7 meters.
Project development:
To finalize the project and to be able to comply with all the client’s requirements, a whole team of experts came together, not only Visa engineering team but also partners, suppliers and client himself.
All the phases were carefully defined and developed one by one.
Special features:
To reduce the noise level in a so big unit it was decided to install a dry cooler on the top of the container roof, equipped with low-noise fans.
Dedicated noise-reduction buffers were installed in the air inlet and outlet channels.
In addition, on top of the roof, a special residential muffler was mounted, more than 5 meters long, 1.1 mt diameter.
Special ventilation was used to cool down the container temperature avoiding any overheating problems.
The openings for air-inlet and outlet are provided through motorized louvers, a solution to keep the container warm during the stand-by phases in winter or in case of cold temperatures.
A dedicated heater blows hot air inside the container allowing to maintain a constant room temperature, approximately around 20 °C.
According to the project indications and to the specific needs of this complex application, we used a special double-wall fuel tanks in compliance with Kiwa standards, complete with special double set of refueling pumps as to grant appropriate redundancy.
A special polishing filter system was installed to avoid development of sludge in the fuel.
Moreover, a dedicated space was designed insider the container to install the fire extinguishing system.
Control panel:
A special dedicated cabinet was developed to cover any application needs.
Two Intellivision 5 by Comap controllers work simultaneously and share a signal which is called “heart beat”.
In the standard operation, the secondary controller is inhibited as long as the primary one is running.
In case of a failure of the primary controller however, the secondary system is able to take the full control. This operation is managed fully automatic without any intervention.
Both controllers can be monitored automatically via Modbus by the customer building management system (BMS).
Fuel tanks
The generating sets were completed with 1 tank of 6000 Liters to grant a great working autonomy, in addition to the on-board tank of 500 liters mounted on each machine.
Test
Prior to delivery the entire system consisting of the 2 units was submitted to a specific test program in accordance to what agreed with the customer to check that everything was perfectly working and in line with the request of the customer.
The application is full of highly technological components granting the best performances and the maximum level of reliability.
The challenge
The big challenge was determined by the strict delivery time stated in the agreement which involved different Visa department (technical department, production, logistic, etc); time schedule had to be accurately monitored. Thanks to Visa Lean Production Management System we were able to carry out this aspect successfully.
It was not easy to combine the delivery of so many components and, at the same time, to manufacture by respecting the strict schedule considering the unexpected situation due to the Covid-19 emergency and restrictions that affected various aspects of item supply.
The fulfillment of the entire project was possible thanks to the partnership among the Visa work team, our reliable and long-term suppliers, as well as the customer himself.