POWER SUPPLY STATION FOR THE ‘PLANS-FRARA’ GONDOLA LIFT PLANT IN COLFOSCO (BZ), ITALY
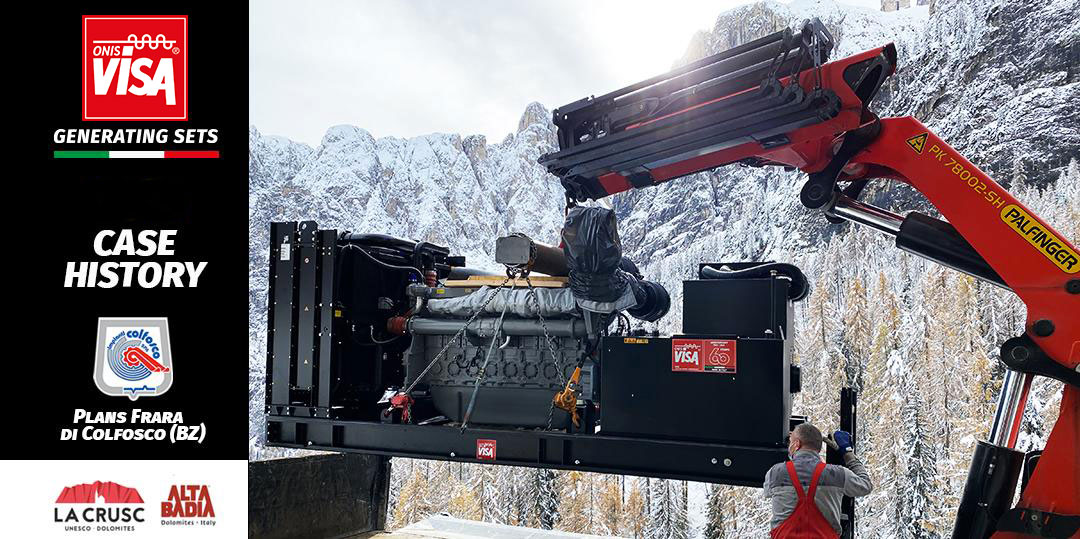
We recently arranged a special application: two units of machines destined to supply the gondola lift plant in Colfosco (BZ), in the Dolomites in case of any power shortage or failure to guarantee the regular operation as well as to allow the safe evacuation of people.
CASE HISTORY
DATA | DESCRIPTION |
---|---|
Project: | POWER SUPPLY STATION FOR LIFT PLANT |
Location: | PLANS-FRARA COLFOSCO – BOZEN (ITALY) |
Power installed: | 2260 kVA (P.R.P.) |
Generating sets: | 2 x P 1150 U |
Dimensions: | 1550 x 4300 x 2460 mm (W x L x H) |
Purpose:
To guarantee the operational continuity of the lift plant by preventing any power outage.
Project's details:
The information in the hands of our engineers to develop this project was actually a figure: the value of the harmonic content in current measured by our customer. This information, together with the total power required by the lifting plant, was the preliminary step which we started from. This information told us how much the electrical load made the waveform of current and voltage particularly deformed. Usually, this type of electrical loads tends to overheat the alternator windings causing the breakdown of the insulation and bursting the alternator. That was what happened to the customer’s generating sets he was going to replace. .
Preliminary analysis:
Thanks to the calculation tools developed by VISA SPA in more than 60 years of experience, combined with professional long-term relationships with our suppliers, we were able to offer the most suitable solution to meet the customer’s requirements. The best option in this case was a genset provided with an oversized alternator with a particular technical feature that made it efficient: a very low sub transitory reactance. A simple evaluation was not enough for the customer, he asked that the solution emerging from the project calculation was then confirmed during the final testing phase and complete with a detailed technical report about the measures performed. The result of the preliminary technical assessment led to select 2 units of gensets model P1150U in open version. Thanks to our high degree of standardization, we could adapt the standard baseframe of genset P1150U to the customer’s application, supplying 2 machines equipped with an oversized MeccAlte alternator of 1400 kVA, mounting control panel in Synch 200 for parallel synchronization. Beside the engine-radiator and alternator, the baseframe also includes: a 400 Liters onboard fuel tank with retention basin to prevent any possible leaking, control panel for monitoring and control and on-board oil extraction pump .
Technical specifications: :
Model P 1150 U, P.R.P. 1130 kVA - 904kW, L.T.P 1250 kVA, 400V, 50Hz. Perkins engine mod. 4008-30TAG3 equipped with tropicalized radiator and coupled with an oversized MeccAlte alternator mod. ECO 43VL4A, of 1400 kVA. The required torsional analyzes assured us that the single-bearing coupling was suitable for this application.
Control panel:
The gensets are provided with In Synch 200 control panel allowing to manage the synchronization between the two units. It is one of our new models of control system which allows the interaction between the control units managing not only the parallel synchronization but also the power management, by sharing the load between the two electricity generators. Communication occurs through CAN BUS protocol of the two In Synch 200 controllers which also manages to detect any anomalies informing the operator through a message both on the display or via email
WebSupervisor: supervision, monitoring and technical assistance service
The project also includes the modern Web Supervisor system for monitoring, control and customized technical assistance, constantly connected in real time through a dedicated platform that always allows the monitoring of the machines, the visualization of the statistics and the sending of notifications via email / SMS for alarms, anomalies and machine maintenance. The gensets are connected to the VISA SPA technical department where they are managed by the qualified staff to detect and solve any problems or anomalies before they turn into dangerous critical issues.
Moreover, included in the supply, the client required also the 24/24 service assistance availability. In this specific project for the Gondola Lift Plant in Colfosco, the WebSupervisor and its software were installed directly in the plant control station, in order to allow the operator to monitor the correct operation and, even more important, to immediately intervene in a direct way in case of need.
Site inspections and positioning of the machines:
We personally went to the lift plant both to arrange the necessary inspections of the technical room and to support the customer in identifying the most suitable and effective positioning of the two gensets. The machines were expected to power the cableway bringing it to a speed of 5 m/s without imbalances or oscillations of the genset. After carrying out the tests in our testing rooms and simulating all the operations of the generating sets, we have prepared the machines for their purpose service. Because of the results we had obtained in the “in-house” simulations, we were sure about the result we would have achieved on site. In coordination with the customer’s consultants, we took part in the installation of the machines inside the technical room. The test at the Gondola Plant was carried out in the presence of the Safety and Cableway Transport in Bozen with scrupulous attention, making the generating sets deliver power up to their maximum limit and the result was successfully obtained with a great margin. The machines that were selected as the result of the design calculations resulted to be the most suitable and led to the desired results.
The gondola plant has reached the required speed fully satisfying the customer’s expectations and the inspectors’ strict requirements, who officially approved it to be used in case of power failure.