EMERGENCY SUPPORT FOR HOTEL APPLICATION
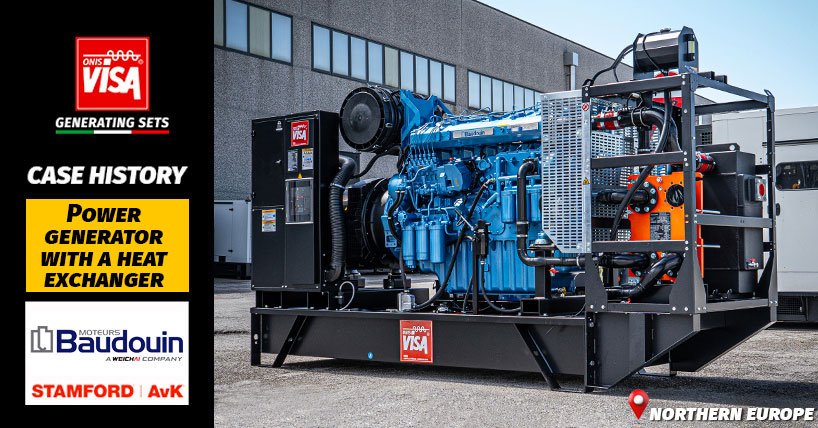
Visa SpA has recently delivered a special project destined to Northern Europe for Hotel sector. It is a genset of 650 kVA that has to comply with some specific requirements stated by the customer.
An emergency generating set is vital in the hotel sector non only because hotels rely on various electronic systems for reservations, billing, and communication, but mainly because a backup generator ensures that safety systems such as emergency lighting, fire alarms, and security cameras remain operational during any power outage, a critical aspect for the safety of guests and staff.
DATA DESCRIPTION
Project: EQUIPMENT FOR HOTEL SECTOR
Location: Northern Europe
Power installed: 650.0 kVA ( PRP) , 715.0 kVA (LTP)
Gensets supplied: 1 unit of BD 650 B model in special version
Purpose:
The project involves a reliable electricity supply system in emergency mode for an hotel installation to maintain operations, ensure guest satisfaction and uphold safety standards during power outages.
Special configuration:
Considering the type of application and the specific requirements of the site, we have designed a machine provided with specific features such as a heat exchanger and two- bearing alternator and a terminal board PW005 to allow the customer to arrange the system with his proper controller.
Technical specifications:
The electricity generator is fitted with a Baudouin engine model 6M33G715/5, 1500 RPM with speed governor and without radiator, and is coupled with a Stamford double-bearing alternator model HCI5F, with AVR MX321 with PMG and droop kit for parallel use. The genset is supplied without control panel. It is in open version.
Control panel
No control panel is assembled on board. The gen set is provided with a terminal board PW 005, to allow the customer to arrange his proper controller.
To meet the requirements of the customer who wanted to connect their cables to the upper part of the panel, the connection between alternator and circuit breaker is made by connecting to the lower part of the circuit breaker.
According to the customer’s specific request, the machine has been provided with cable entry from above.
Alternator
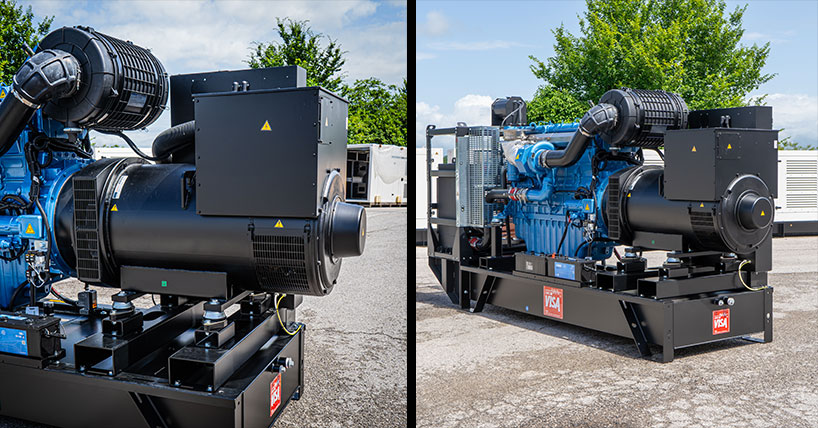
The gen set is equipped with a Stamford double-bearing alternator. The alternator shaft is supported by two bearings making the machine more robust.
This system helps reduce the transmission of vibrations between engine and alternator and it is particularly suitable for avoiding torsional problems, particularly when the alternator is oversized in relation to the engine power.
In fact, this type of installation provides for the connection between the engine and the alternator using an elastic coupling which, when deformed, absorbs part of the torsional vibrations by preventing their transmission between the engine and the alternator.
In the front part, the alternator shaft is coupled to the engine with the flexible coupling to absorb the vibrations produced by the load.
In some cases, a double-bearing alternator is preferable due to its ease of disassembly and maintenance, quick swap speed, and reduced damage during short circuits or block events, despite its higher cost and increased overall size due to the addition of components like the front bell/shield and coupling.
Heat exchange system:
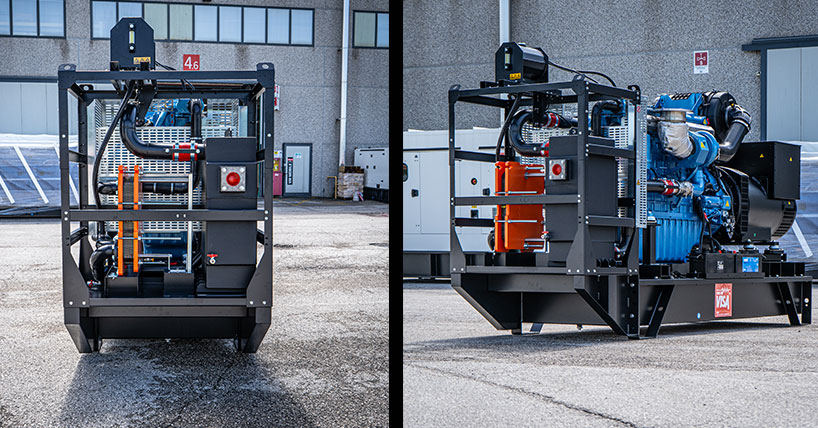
Instead of the radiator, the genset is equipped with a heat exchange kit which allows the engine to be cooled using a remote radiator.
Since the genset is positioned in an area where the air flow is limited, a proper cooling system is required.
The engine is cooled through the cooling kit, a heat exchange kit designed to transfer the heat generated by the engine to a dry cooler positioned in an external area of the building away from the genset.
The cooling kit consists of two main components: a plate heat exchanger for cooling the engine water jacket and an air-to-water exchanger for cooling the charged air (CAC, charged-air cooler).
From this stage, the hot water is transferred through a pump from the secondary side of the kit up to the dry cooler located in the external part of the building, assuring the system to work properly with the right air flow.
This type of solution is increasingly common for installations of generator sets in premises which do not have sufficient openings to ensure a correct cooling of the engine (or to reduce the noise impact of the genset).
Conclusions :
The generating set will be housed in specific place, prepared by the customer with all the appropriate features that allow it to work properly.