Data Center Sector: 4x1700 kVA Onis Visa Power Container
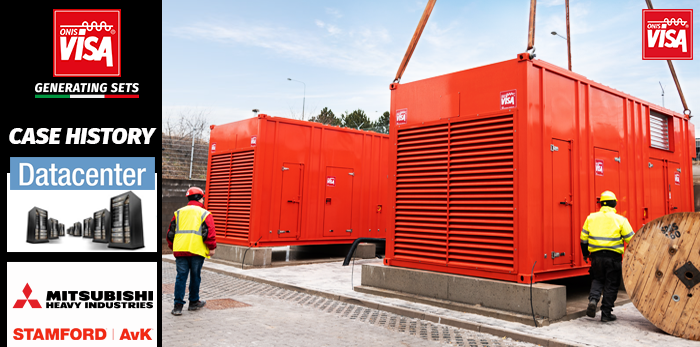
Visa SpA has been recently involved in a high-profile project of supplying generators for a Data Center ensuring un interrupted power supply, strictly complying with the specific and high-demanding requirements of customer. The generators have been designed by our specialized team of engineers in cooperating with our highly experienced distributor to provide reliable power in case of power outages due to utility grid failures, inclement weather, blackouts, natural or man-made disasters that can put data center at risk of operational loss.
The project, which requires a high complexity in its engineering and conception, has been divided into various stages, from conception to final installation, involving 4 total machines. Model M 1700 generator sets in container version have been selected as the most suitable to power the project, two in red and two in white color.
Challenging aspect of the project:
This data center project was complex and demanding and our team found it very inspiring to be able to find the best solutions to fulfill the customer’s strict requirements.
Over the last few years we have increased our focus on power back-up for datacenter applications, proposing every time more advanced and up-to-date solutions to totally guarantee the infrastructure running smoothly even in cases of any disturbances and always having clear in mind the vital role that power plays in data centers.
Purpose:
The project involves a reliable electricity supply system in emergency service to ensure that everything runs smoothly in the plant at all times, counting on a steady supply of uninterrupted electricity on a constant basis.
Given the critical nature of the application, machines have been developed with all the appropriate features to ensure maximum safety and to allow it to work properly, perfectly knowing that a sudden loss of power can cause a loss of data, corrupted files and equipment damages.
DATA | DESCRIPTION | |
---|---|---|
Project: |
|
|
Location: | EUROPE | |
Power installed: | 6.8 MW | |
Generating sets supplied: | 4 units x M1700 Power Container Custom |
Video:
Special configuration:
Since the beginning the project has proved to be very challenging considering the type of application and the specific requirements of the site, where redundancy system and extremely high reliability were considered the priority. Moreover, the site needed contained sizes because of problem of space.
The request was to host 4 units of 1700 kVA of PRP power each, in an oversized container with special dimensions (length 6600 x width 3000 x height 3500 mm) and a noise level of 85 dBA @ 1 mt.
Technical specifications:
All 4 gensets have been fitted with Mitsubishi engine model S16R-PTA, 1500 Rpm, with engine pre-heater, and Stamford alternator model PI734E – Class H with a MX341 AVR and an anticondensation heater. The machines are conceived for parallel operations and are equipped with automatic paralleling among gensets control panel in container. 400 Litres integrated fuel tank.
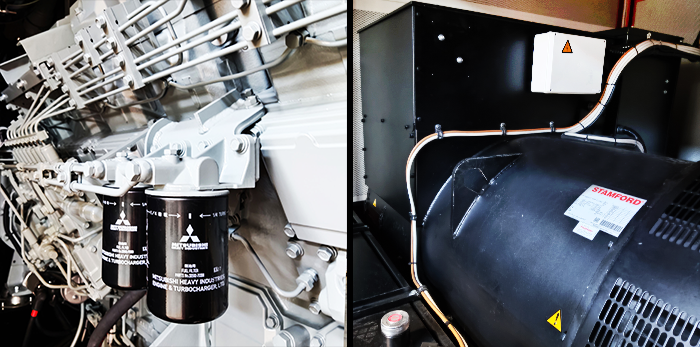
Starting system
The engine is provided with a redundant starting system. A third starter was added in addition to the 2 standard ones. Each genset is also fitted with 2 sets of starting batteries with disconnector switches and 2 batteries chargers. The alternance of the battery sets is managed by the control panel at each starting attempt while the 3 starters are always simultaneously engaged.
Control panel
The control cabinet of each genset hosts a Comap IG-NTC BB with IV5. According the specific customer’s request, the cabinet had to be oversized in order to have some additional available space inside, for installing a touch-screen display directly by the customer, to control the fuel pumps and the communication with the BMS.
Layout:
Considering the dimensions of the plant and the issue about the reduced space available (in particular, the length had to be as short as possible), the project was deeply discussed. The final solution came out after many hours of cooperation among our team of engineers, our well-experienced distributor and the final customer taking into consideration the peculiar aspects of the installation site. More specifically, all the containers were to be placed on 3 beams which were 400 mm higher than the level of the operator on the ground.
Furthermore, an ultra-compact baseframe was designed in order to save space and make maintenance operations easier and more accessible inside the container.
The container is provided with an electrical system including standard and emergency lights as well as service plugs.
Heat recovery system
While the gensets are in stand-by mode, the engine is kept warm by the combination of a standard heater and a heat recovery system supplied by the customer. The heat recovery system takes advantage of part of the heat dissipated by the data center to warm the engine via a plate heat exchanger.
In order to reduce the heat dissipation of the container in stand-by mode, a motorized louvre was installed on the air inlet of the engine compartment, as well as two gravity louvres were installed on the air outlet. The motorized louvre is controlled by the genset control panel and the gravity louvres are driven in open position by the two cooling fans.
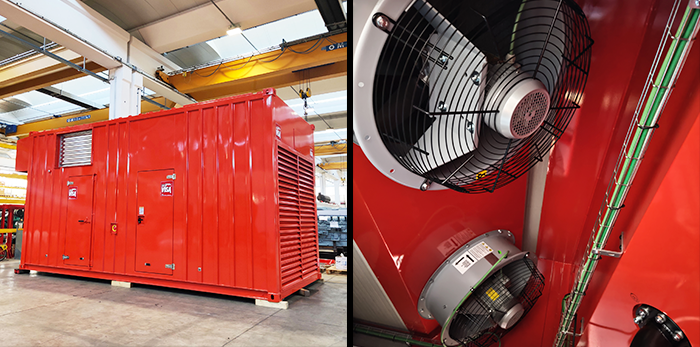
Cooling system:
The engine compartment is cooled by 2 fans. An air outlet channel with sound attenuators was created above the engine in order to convoy outward the hot air and to reduce the airborne noise. A hatch was created in the ventilation channel in order to make it accessible for maintenance purposes.
Radiator:
In order to reduce the noise level, the radiator was placed in front of the container, in a dedicated compartment with 2 pushing fans expelling the hot air above the roof.
A bulkhead separates the radiator and the engine compartment preventing the noise propagation and to mix the air flow of the radiator with the one of the engine.
Find out more at : www.visa.it